甘露醇的傳統提取工藝
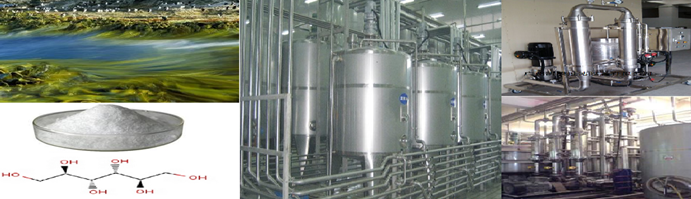
一、傳統工藝水重結晶法
從海帶提取甘露醇的傳統工藝是水重結晶法,具體工藝流程如下圖所示,該工藝存在如下弊端:
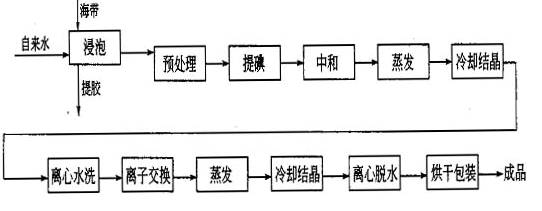
1. 海帶中甘露含量通常在1%左右(按放水倍數10-12%),而其結晶濃度在20%左右,必須從海帶浸泡水中蒸發掉大量水分才能使甘露醇興奮結晶析出。而且頭液要經過兩次蒸發濃縮和結晶過程,即有兩次變相過程。因此能耗高,每制取1t甘露醇需耗蒸汽60t左右。
2. 由第一次濃縮結晶得到的粗品需要重新用水溶解后,采用離心水洗等方法除去糖膠等有機雜質和無機鹽,但同時甘露醇也被溶解流失,得率損失10%左右。
3. 海帶浸泡液中含1%左右的甘露醇外,還含有3%的無機鹽,主要是NaCl(鹽鹽中和法)或Na2SO4(硫酸中和法)和一定的硬度離子。若是NaCl,則Cl-會對不銹鋼材質的蒸發器產生嚴重腐蝕,如若Na2SO4則會引起蒸發器結垢。均會縮短蒸發器的使用壽命,增大設備的維修和更換費用,還會給生產帶來不安全因素。
4. 自動化程度低、工人勞動強度大,生產環境惡劣。
二、膜集成工藝
膜集成技術提取甘露醇工藝系統由料液預處理、UF凈化、ED一次脫鹽、RO濃縮和ED二次脫鹽等五部分組成。工藝流程如右圖所示。
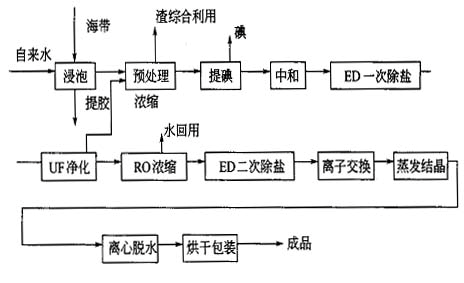
1.料液預處理系統
提碘后的海帶浸泡水先所經過絮凝和動力形成膜自動恒壓式硅藻土過濾機進行固液分離,透過液SDI控制在4-6之間。
2.電滲析一次脫鹽系統
經硅藻土過濾機過濾后的海帶浸泡液無機鹽濃度一搬介于18000-22000mg/L左右,這些無機鹽在RO濃縮甘露醇時,也會同時被濃縮。同時高鹽度浸泡液濃縮時過高的滲透壓力,限制甘露醇濃縮倍數,因此需要采用EDI預脫鹽,經電滲析EDI預脫鹽后浸泡液電導率介于2500-3000us/cm(25℃)以下。
3.超濾系統
超濾UF作為RO的預處理系統,去除浸泡液中的懸浮物、大分子有機物、溶解性顆粒等雜質。甘露醇相對分子量為182,其它溶解性雜質主要為褐藻糖膠及聚合體,相對分子量大于50000。因此系統選用截留分子量為1-3萬的超濾膜,表面呈負電荷的聚砜材質中空纖維膜。由于浸泡液含有大量的膠體、蛋白質、多糖類有機物及無機鹽,容易造成UF膜堵塞,因此系統配置專用CIP在線清洗系統。
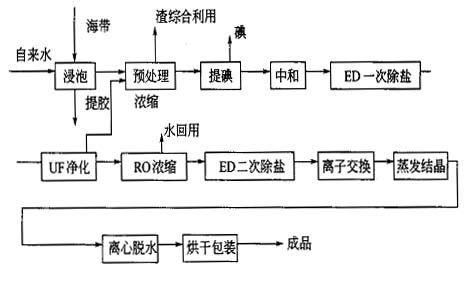
4.反滲透RO濃縮系統
UF透過液SDI控制在2-4之間,滿足反滲透RO膜元件水質要求。經UF過濾浸泡液含甘露醇濃度介于1.3-1.5%,RO濃縮脫水3-5倍以上,RO濃縮系統采用進口圈式抗污染反滲透復合膜,配套加壓系統、儀表控制與監測,設計流程參考下圖:
5. 電滲析二次脫鹽系統
料液經過反滲透裝置濃縮后甘露醇濃度濃縮達到3倍,料液中的無機鹽也同時被濃縮3倍。這樣在后工序精制過程中,直接采用離子交換除鹽負擔過重,需要頻繁再生。為此采用離子交換膜ED對濃縮液進行第二次脫鹽。脫鹽后的料液再次經離子交換二次脫鹽。料液經第二次脫鹽精制后,出水含量為140mg/L左右,進入下道成品工藝。
上述工藝流程中的核心部分,UF和RO系統采用計算機監控,操作運轉和管理非常簡便。
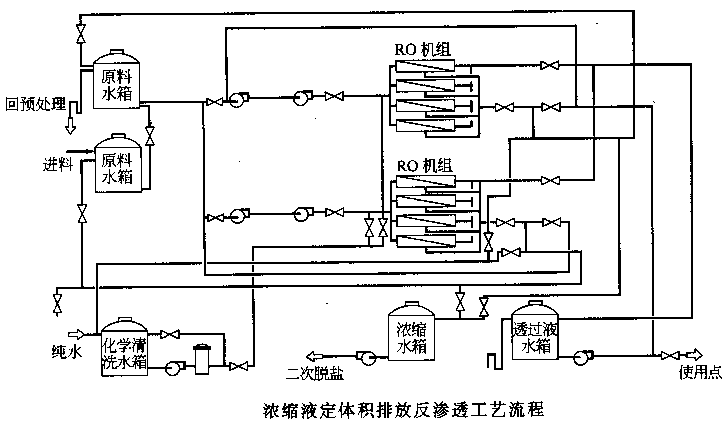